AAC Blocks
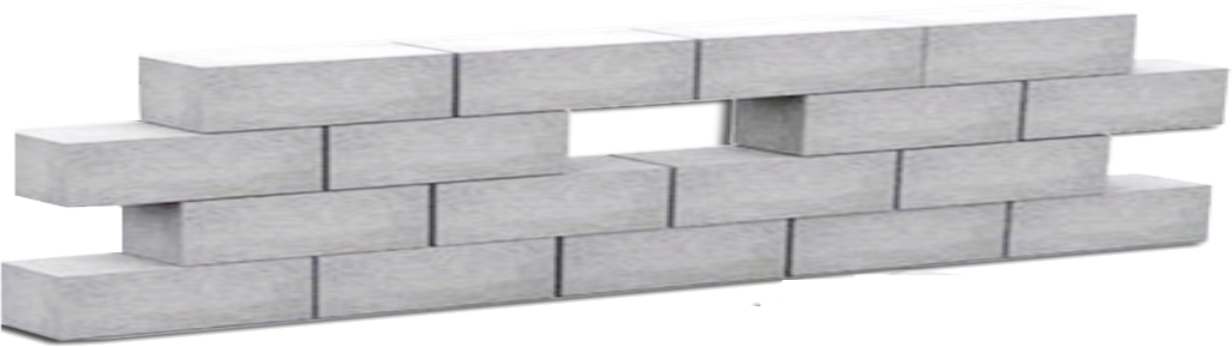
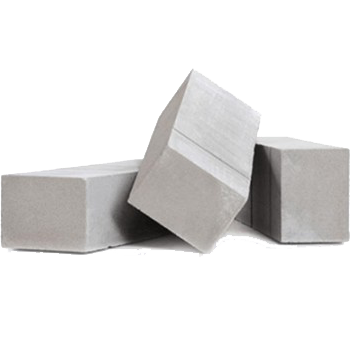
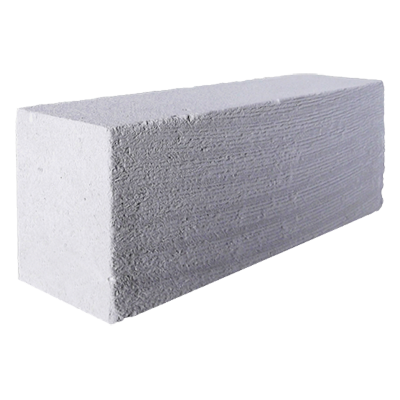
What is AAC?
The Autoclaved Aerated Concrete (AAC) material was developed in 1920 in Sweden. It has become one of the most used building materials in Europe and is rapidly growing in many other countries around the world.
Autoclaved Aerated Concrete is a lightweight, load-bearing, high-insulating, durable building product, which is produced in a wide range of sizes.
AAC offers incredible opportunities to increase building quality and at the same time reduces costs at the construction site. AAC is produced out of a mix of pulverized fly ash (PFA), lime, cement, gypsum, water, aeration compound and is hardened by steam-curing in autoclaves. As a result of its excellent properties, AAC is used in many building constructions, for example in residential homes, commercial and industrial buildings, schools, hospitals, hotels and many other applications.
Advantages of AAC Blocks

Sound Resistant
AAC blocks can provide very good sound insulation / sound absorption with an STC rating of 44.

Thermal Comfort
AAC is excellent thermal insulation properties result in improved comfort level and saves heating and cooling costs.

Fire Resistant
More superior than traditional masonry for products with fire resistant up to 4 hours for a nominal block thickness of 100 mm.

Eco-friendly
AAC to help reduce at least 30% of environmental waste, decrease 50% of greenhouse radiation

Cost-effective
Speed and ease of installation result in cost savings compared to traditional masonry construction

Impact Resistant
Wall erected using 100 mm thick are to withstand impact loads potentially resulting from rough usage.

Durable
Histories of usage dated more than 50 years protecting building and remain durable even under extreme weather conditions.

Dimensional Accuracy
Blocks using modern machineries resulting in products with tighter dimensional tolerances.
Dimension of AAC Blocks
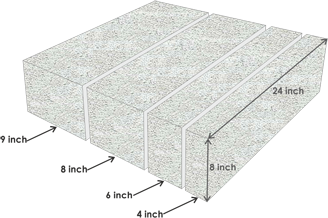
Density of various Materials
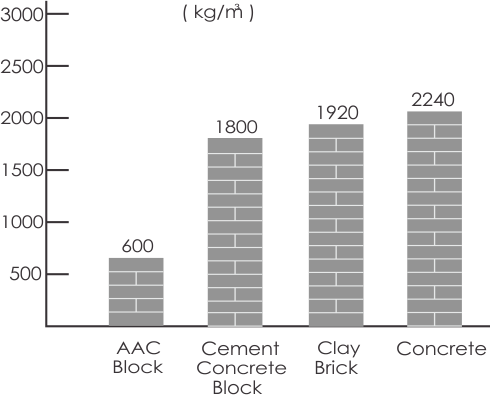
Facts of AAC Blocks

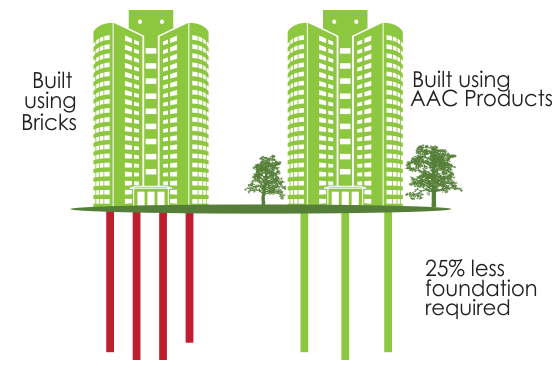
Save up to 25% of Foundation Cost
Great savings in foundation and structural costs due to decrease in overall dead load.
Due to light weight and low density, overall dead load reduces, thus saving structural steel consumption compared to conventional masonry.
Read More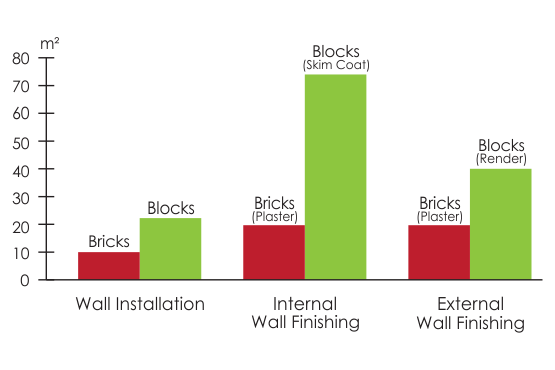
Wall Installation Speed
AAC Block vs Brick (m²/ workers/ day)
AAC blocks are seven times the size of traditional bricks. These results in substantial savings in Cement due to fewer joints compared to brick work and finished plaster work.
Faster construction gives higher work productivity.
Read More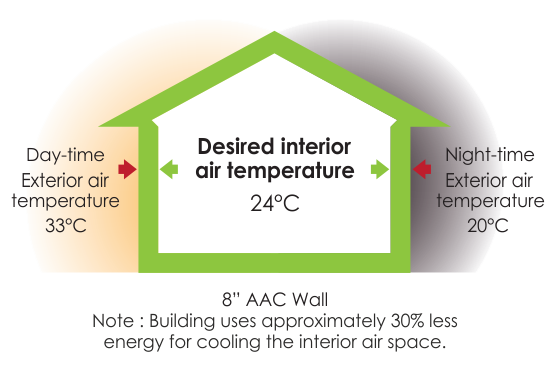
Thermal Control
Heat insulation 6 times superior than clay brick.
Due to the numerous micropores in AAC, it has a very low thermal conductivity and makes an excellent thermal insulation material.
It keeps interiors cooler in summer and warmer in winters.
Read MoreTechnical Specification
Property | Units | AAC Block | Clay Brick |
---|---|---|---|
Size | mm | 600 X 200 X (100 to 300) | 230 X 75 X110 |
Compressive Strength | N/mm2 | Min 3 * | 2.5 to 3 |
Normal Dry (Oven Dry) Density | Kg/m3 | 551 to 650 * | 1800 to 2200 |
Thermal Conductivity "K" | W/m-k | Max 0.24 * | 0.81 |
Drying Shrinkage | % | Max 0.05% * | - |
Fire Resistance | Hrs. | 2 to 6(Depending on thickness) | 2 |
Sound Reduction Index | Db | 45 for 200 mm thick wall | - |
* As per IS 2185 Part 3 |
Comparison between AAC Block and Clay Brick
Parameter | AAC Block | Clay Brick |
---|---|---|
Structural Cost | Steel saving upto 15% | No saving |
Cement Mortar for
Plaster & Masonry |
Required Less due to flat, even surface and less number of joints |
Requires more due to lrregular surface and more number of joints. |
Breakage | Less than 4% | Average 10 to 12% |
Construction Speed | Speedy construction due to its
big size, light weight and easy to cut in any size or shape. |
Comparatively slow |
Quality | Uniform & Consistent | Normally varies |
Fitting & Chasing | All kind of fitting and chasing possible | All kind of fitting and chasing possible |
Carpet Area | More due to less thickness of walling material | Comparatively Less |
Energy Saving | Approx. 30% reduction in air-conditioned Load | No such saving |
Chemical Composition | Flyash used around: 65 to 68% which reacts with lime and cement to form AAC |
Soil used contains many inorganic impurities like
sulphate etc. resulting in efflorescence |
Call Us
AAC
We offer high quality and precisely designed blocks manufactured with Autoclaved Aerated Concrete (AAC).
CONTAC US
info@agps.in
No 4, 10th Main Road, Peenya 3rd Phase
Laggere, Bengaluru, Karnataka
Light Weight Concrete Block Dealers
Light Weight Concrete Block Distributor
Aac Block Manufacturers
Aac Block Dealers
Aac Block Distributor
Fly Ash Blocks Manufacturers
Fly Ash Blocks Dealers
Fly Ash Brick Distributors
Aac Block Ultra Tech
AAC Block Karnataka
Light Weight Concrete Block Aerocon
Light Weight Concrete Block Biltech
Light Weight Concrete Block Siporex
AAC Blocks in Bengaluru
Siporex
Ultra Tech
Adyalite
Magicrete
Renacon
Fusion
Aerocon
Light Weight Concrete Block
Light Weight Concrete Block Manufacturers
Aac Block Fusion
Aac Block Adhesive Dealers
Light Weight Clay Brick Manufacturers
AAC Blocks in Karnataka
Aerocon Block
Fly Ash Blocks
Fly Ash Brick
Concrete Block Aerocon
Cement Block Siporex
Fly Ash Dealers
Fly Ash Brick Manufacturers
Fly Ash Brick Wholesalers
Light Weight Concrete Brick
Fly Ash Brick Karnataka
Aac Block Adyalite
Aac Block Magicrete
AAC Block Renacon